The Changing Demands of the Mid-sized Drilling Contractor
By Bob Martin - General Manager - August 1, 2009 - Featured in Trenchless World Magazine
These changing economic times have certainly thrown the world on its ear, in some places more than others. Contracts have been delayed or shut down altogether, and in areas where the work does exist the ability for a contractor to obtain funds for the purchase of equipment to complete the work has diminished substantially. Through all of this, however, the needs and wants of the contractor remain unchanged. Manufacturers have, over time, invested considerable time, energy and resources in to the evolution of the HDD drill, and we have seen the results over the last few years.
2001 saw considerable advancements in the area of directional drill technology when Ditch Witch came out with their Mach 1 line of directional drills. These units were faster, easier to use, and more productive than their older counterparts, and demand for them skyrocketed. Shortly thereafter, they also announced their line of AT rock drilling machines. Vermeer answered the competition by unveiling their line of Series II Navigator drills, which offered many of the same features and satisfied their own customer base.
What, exactly, was it that customers were looking for? For the most part, both companies addressed the same issues in similar ways. First off, the advantages of rack and pinion pulldown versus the previous generation's use of chains were employed which included longer life, higher reliability and more efficient transfer of power to the carriage. Other manufacturers had used the rack and pinion system for decades, however the use of it in drills smaller than those used in river crossings began to the greatest degree during this changeover by the largest two manufacturers.
Advancements in hydraulics and computer control also allowed higher carriage speeds to be employed, making the shuttling of pipes a far faster process and increased productivity. Similarly, advancements in engine and turbocharging technologies allowed much more powerful engines to be employed in smaller packages, putting more power into smaller footprints. With more power came the ability to utilize higher-capacity mud pumps and the mud pump technology itself also allowed for higher duty cycles and lower frequency of maintenance.
Most of the major manufacturers also switched from a solid steel engine cowling to a more ergonomic one-piece fiberglass enclosure that offered superior sound dampening and far greater ease of access to the engine, cooling, and hydraulic systems.
From the operator's standpoint, the actual operator's stations were redesigned for ease of use, greater comfort and better field of vision. Many of the larger mid-sized drills also began to offer cab options as well, allowing the use of heaters or air conditioners for areas with adverse weather conditions. New technologies that allowed for automatic monitoring and adjustment of pullback and rotation pressures reduced the amount of operator fatigue and appeared under such banners as "Auto Drill" and "Cruise Control".
Also identified as a need and want in this mid-sized market was an economical alternative to mud motors for rock drilling. Several suppliers of tooling, both OEM and aftermarket, came up with tooling designs revolving around the drilling of rock. Some of this tooling was moderately effective in softer rock formations, however in order to be competitive, an alternative method of drilling in rock was needed. Vermeer came out with their RATT (Rock Adaptable Terrain Tool) system and the RS series tools, which offer rock drilling capabilities using conventional drill stem to power it. Alongside this was Ditch Witch's offering, their complete line of rock drilling machines which they dubbed the All Terrain Mach 1. These drills utilize a specialized gearbox capable of powering both an inner and an outer rod. Rather than using fluid to power a motor, the machine's power is sent through a dedicated inner shaft directly to the drill bit. Advancements such as these have put rock drilling capability within the reach of contractors who did not have the resources to tool up a larger machine along with all of the related peripheral equipment necessary for mud motor rock drilling.
All of these changes, and some others not mentioned here, combined to create a new breed of directional drill. The new drills were faster, more productive, easier to use and have a higher reliance upon electronics, computers and sensors in order to operate correctly. Owners of these machines often find it in their best interests to ensure that properly trained service personnel are available at all times, either through their own employee resources or through the local dealerships. Troubleshooting issues in the field is typically more problematic on the newer machines than on the older ones that had much simpler designs.
This tradeoff has really seen two different groups of buyers emerge, those with the need and desire to own and operate the latest and most productive machines, and those putting more value upon reliability and ease of service and maintenance. Areas with good access to parts and trained service personnel will typically see a higher concentration of buyers looking for the newest machines. Such areas may include North America and Europe as examples. On the other end of the spectrum, buyers who have little access to parts and without specialized service personnel often favor the simpler line of equipment that was typically seen in the late 1990's and early 2000's. Parts for these machines are cheap and plentiful, and diagnosing and repairing issues is well within the realm of any moderately skilled technician. Developing countries with poorer economies but with a strong demand for HDD technologies favor this style of drill.
The used market sees both types of equipment, new and old. A production gap that took place within North America between late 2001 and early 2004 as a result of the fiber optic crash created a very noticeable point from which to reference the approximate time that the shift from the older, simpler machines to the newer, faster and more complicated machines occurred. Typically, new models find their way to the used market within 12 to 18 months of its original sale for various reasons.
Along with productivity and user-friendliness differences, there is also a marked difference in the price of the two types of drill.
For example, based on current listings on the used equipment website, www.hddbroker.com, Ditch Witch JT2720 drills are currently being sold with an approximate average price of $45,000USD, the slightly newer JT2720M1 drills at $70,000, and the JT2720AT at $80,000 (all based on current listings as of the writing of this article). Moving up into the replacement for the JT2720 lineup, a used JT3020M1 sells for an average of $170,000, while the AT version of the same machine sells for $240,000. That is a difference of $100,000 to upgrade from the JT2720M1 to the JT3020M1 and $160,000 to upgrade from the JT2720AT to the JT3020AT.
Similarly, when talking about Vermeer drills, the Vermeer D24x40A currently averages at $46,000USD while the newer D24x40 Series II machine sells for approximately $120,000, a difference of $74,000.
Obviously we are not comparing "apples to apples" so to speak, as the older drills will have comparably higher hours than their newer counterparts, however the point that is being made is that from a purely monetary standpoint there is advantage to some companies to move forward with an older, less expensive machine, particularly when factoring in the availability of parts and ease of maintenance and repair.
Another factor to consider is that there are current new offerings for simple machines that see quite significant price differences versus the most technologically advanced units from the major manufacturers. These units offer the benefit of full factory warranty while still retaining simplicity of repair and maintenance, and have found a niche in both developing countries and those with stronger economies.
Each contractor will have an opinion based upon their own needs, and those needs will be shaped by the environment that they work and live in. What is right for one company will not be so for another. Every advancement made in the technology that a drill incorporates has an impact on other aspects of the drill, be it price, repair costs, the frequency of repair or maintenance and other areas. The big question is whether the advancements are enough of a benefit to outweigh the drawbacks.
The last half decade or so have seen exciting changes in the drill market offerings, and there will no doubt be many more in the years ahead. The market will see its share of demand for the newest and greatest machines, but it will also see continuing demand for simpler, less advanced machines as well. Without a significant advance in the overall technology used to drill, that should remain unchanged for a while to come.
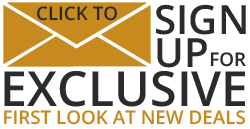
This commentary is presented for informational purposes only. It is not intended to be a comprehensive or detailed statement on any subject and no representations or warranties, express or implied, are made as to its accuracy, timeliness or completeness. Nothing in this commentary is intended to provide financial, legal, accounting or tax advice nor should it be relied upon. Neither HDD Broker LLC nor the author is liable whatsoever for any loss or damage caused by, or resulting from, any use of or any inaccuracies, errors or omissions in the information provided.